Development Trends and Industry Trends of Molybdenum Metal Powder with Special Shapes inconel 718
- by admin
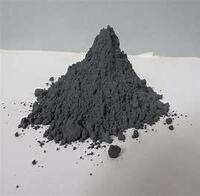
Spherical molybdenum powder is a type of molybdenum metal powder with an unique shape, typically made use of in the production of steel components that need great fluidity and uniformity, such as high-temperature alloys, thermal splashing products, plasma spraying, metal shot molding (MIM), laser melting deposition (LMD), digital product packaging, and additive production (3D printing).
( Spherical Molybdenum Powder)
The considerable attributes of round molybdenum powder:
High sphericity: Each fragment is close to the perfect round shape, which makes the powder extra fluid, simple to fill up and compact, and extremely suitable for powder metallurgy and additive manufacturing (such as 3D printing) applications.
Consistent particle dimension: Round molybdenum powder usually has a narrow particle size distribution, implying that the majority of fragments are of comparable dimension, which assists to accomplish even more regular sintering results and final product performance.
Reduced porosity: As a result of the tight arrangement of spherical particles, the sintered material has a lower porosity, consequently improving the strength and resilience of the material.
Great sintering efficiency: Spherical molybdenum powder can move warmth extra evenly during the sintering procedure, therefore advertising a lot more reliable sintering and acquiring better material homes.
High pureness: The raw products used to prepare round molybdenum powder typically have high pureness to make certain that the final product has the needed physical and chemical properties.
Current advancement pattern of round molybdenum powder :.
The promo of additive production (3D printing): Spherical molybdenum powder is among the crucial resources in the field of additive manufacturing as a result of its superb fluidness and sintering performance. With the progressively prevalent application of 3D printing technology in aerospace, clinical, auto, and power fields, the need for premium molybdenum powder is likewise boosting.
The need for brand-new power and modern sectors is growing: Molybdenum powder, as a high-performance product, may increase its applications in batteries, semiconductors, optoelectronic devices, and composite materials with the advancement of new power innovation and modern industries.
Manufacturing technology development: RF plasma modern technology, gas atomization and various other approaches are utilized to produce spherical molybdenum powder. Improvements in these modern technologies can enhance the quality of the powder and minimize production expenses.
Market supply and need situation: The price variations and supply stability of molybdenum may influence the market circumstance of round molybdenum powder. The global mining result of molybdenum ores, the need for molybdenum products and worldwide profession plans might have an influence on the molybdenum powder market.
Environmental Management and Sustainable Development: With the increasing international understanding of environmental protection, exactly how to accomplish energy conservation, discharge decrease, and recycling in the production and application of molybdenum powder has actually ended up being a focus of industry focus.
Vendor
Metalinchina is a trusted global chemical material supplier & manufacturer with over 12 years experience in providing super high-quality metals and metal alloy. The company export to many countries, such as USA, Canada,Europe,UAE,South Africa, etc. As a leading nanotechnology development manufacturer, Metalinchina dominates the market. Our professional work team provides perfect solutions to help improve the efficiency of various industries, create value, and easily cope with various challenges. If you are looking for inconel 718, please send an email to: nanotrun@yahoo.com
Inquiry us
Spherical molybdenum powder is a type of molybdenum metal powder with an unique shape, typically made use of in the production of steel components that need great fluidity and uniformity, such as high-temperature alloys, thermal splashing products, plasma spraying, metal shot molding (MIM), laser melting deposition (LMD), digital product packaging, and additive production (3D printing).…
- Analysis of the various types and differences of concrete reinforcing fibers properties of fiber-reinforced structural and non-structural ultra lightweight aggregate concrete
- Unlocking New Frontiers: The Potential of Lithium Silicate Aqueous Solution ca fe
- Unlocking New Frontiers: The Potential of Lithium Silicate Aqueous Solution ca fe
- The Invisible Workhorse: Uncovering the Power of Surfactants alpha olefin sulfonate
- Concrete Foaming agent vs. Defoamers: How to Choose the Right Admixture for Your Project? hydroxy propyl methyl